![]() |
Microelectronics Packaging Robotics Cryogenic MEMS Microphones Aeroacoustic MEMS Array MEMS Shear Stress Sensors MEMS Ultrasound Sensors |
Cryogenic Operation of MEMS Microphones for Superconducting Magnet Quench Detection
Collaboration with Luisa Chiesa in the Superconductivity Lab at Tufts, Makoto Takayasu at MIT Plasma Physics Lab, and Michael Emerling, Amish Desai and Steve Chau of Tanner Research
Students: Zijia Zhao, Casey Owen, Mischael Anilus, Jillian Stern
A linear array of MEMS acoustic sensors operating in the coolant space of a force-cooled CICC (Cable In-Conduit Conductor) is an attractive alternative to conventional quench detection techniques. MEMS acoustic sensors are particularly suited for HTS conductors as they can provide high detection speed, good sensitivity, and the ability to localize quench events. In order to implement such a system, MEMS acoustic sensors that can operate in cryogenic fluids (77 K liquid nitrogen, low temperature gaseous and liquid helium) are required. In this work, commercial MEMS microphones and microphone preamplifiers are characterized in cryogenic gaseous helium at static pressures between 0.5 and 1.5 bar, and temperatures down to 20 K, as well as in liquid nitrogen at 1 bar and 77 K. Calibrated acoustic sources are used to deliver plane pressure waves into the cryogenic acoustic media in a plane wave tube geometry. Frequency response data is gathered for several MEMS options: three capacitive MEMS microphones, one piezoelectric MEMS microphone, and a reciprocal electrostatic MEMS speaker used as a sensing element. Distinctions among those MEMS options are drawn regarding the impact of the cryogenic environment on the transducer itself, and on the performance of the required preamplifier electronics. Recommendations of a linear MEMS sensor array method are made for a quench detection and its localization tool in high-current HTS CICC cables and magnets.
![]() |
![]() |
Representative Publications:
Video of a conference talk:
![]() |
Cryogenic Testing of MEMS Microphones for Superconducting Magnet Quench Detection December 2020 at Acoustics Virtually Everywhere conference. |
Representative Publications:
Zijia Zhao Peter Moore, Casey Owen, Mischael Anilus, Steve Chau, Amish Desai, Michael Emerling, Luisa Chiesa, Makoto Takayasu, and Robert White,
“Characterization of MEMS Acoustic Sensors and Amplifiers in Cryogenic Fluids for Quench Detection Applications in HTS CICC,”
in IEEE Transactions on Applied Superconductivity, vol. 31, no. 5, pp. 1-5, Aug. 2021. doi: 10.1109/TASC.2021.3062784. LINK
MEMS Surface Shear Sensors for Aerodynamic Applications
This project aims to develop “direct” surface shear stress measurement sensors that can provide real time measurement of the time resolved local shear stress at the surface of a wind tunnel model or vehicle during ground or flight testing. The goal is to provide spatial resolution of 1 mm, bandwidth of 100 kHz, and to cover the shear stress range of 0.1 Pa to 1000 Pa. Our approach is to micromachine floating element style MEMS shear stress sensors in arrays, and to integrate these with high performance capacitance to digital converters in a small form factor package. There are challenges associated with low topology packaging of the sensors, and sensitivity to other variables such as fluctuating pressures, pressure gradients, and environmental variables such as temperature and humidity. Collaborators have included industry and government partners.
The current design employs 256 “floating element” style sensors on a 1 cm x 1 cm chip. The sensor has been able to measure shear stresses from approximately 0.5 Pa to approximately 15 Pa in laminar flow cell and turbulent boundary layer environments. Current bandwidth is limited to about 10 Hz. Sensitivity to pressure gradient has been characterized. Additional characterization of environmental sensitivities to temperature, humidity, vibration, and fluctuating pressures are needed. Additional developments to improve resolution and bandwidth, as well as reduce surface topology, are under way.
We have applied the array to the measurement of boundary layer shear in a flat plate subsonic wind tunnel study. We are interested in extending our applications areas to additional wind tunnel studies with structured models, flight testing, and turbomachinery.
![]() |
![]() | |||
SEM image of the MEMS shear sensor chip. |
Photograph of the packaged die in its final form factor. |
Representative Publications:
Nikolas Kastor, Zhengxin Zhao, and Robert D. White, “Multiphysics
Model Investigating Performance of a Micromachined Floating Element
Shear Stress Sensor”, Sensors and Actuators A: Physical,
Volume 269, 2018, Pages 1-13, ISSN 0924-4247. https://doi.org/10.1016/j.sna.2017.11.004
Zhao, Z., Shin, M., Gallman, J. M., and White, R. D. “A
Microfabricated Shear Sensor Array on a Chip with Pressure Gradient
Calibration”, Sensors and Actuators A: Physical, Volume 205, 2014, Pages 133-142, ISSN 0924-4247. LINK PDF of the paper.
Zhao, Z., Long, K., Gallman, J., and White, R.D. “Flow Testing of
a MEMS Floating Element Shear Stress Sensor”, AIAA2014-1235, in the Proceedings of
the 52nd AIAA Aerospace Sciences Meeting, National Harbor, MD, January
13-17, 2014. PDF of the
paper.
Robert D. White and Zhengxin Zhao, U.S. Patent 9,964,476, “Shear Sensor Array”, issued May 8, 2018.
Ultrasound Transducers
This project aims to develop and characterize MEMS ultrasound transmit and receive array-on-a-chip devices for navigation and flow sensing applications. The goal is to demonstrate the ability to measure 3D velocity and distance to an acoustic reflector using frequency modulated continuous wave Doppler ultrasound or pulsed chirps. The project includes design, microfabrication, and testing.
The current system has been successful at measuring 1D velocity of a moving reflector with 60 velocity updates per second, at a resolution of approximately 0.5 cm/s and a maximum measurable range to the reflector of 1.5 meters. Work is ongoing in increase resolution, increase range, extend the technology to measure 3D velocities and distance vectors, and reduce package size and power for portable applications. We are interested in collaborating with potential end users who would find a low power, low weight distance and velocity measurement system useful. We can imagine applications in mobile robotics and personal navigation systems.
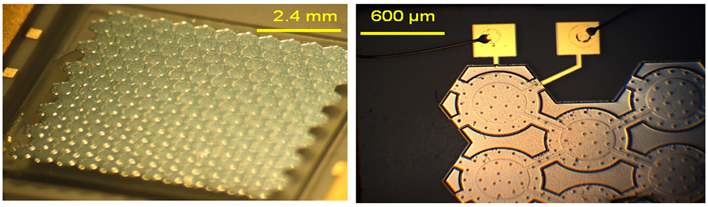
Images of the packaged ultrasound array chip (left), and a microscope image of a few sensor elements (right).
Representative Publications:
Minchul Shin, Zhengxin Zhao, Paul DeBitetto, Robert
D. White, “Micromachined ultrasonic Doppler velocity sensor using
nickel on glass transducers”, Sensors and Actuators A: Physical,
Volume 208, 1 February 2014, Pages 37-49, ISSN 0924-4247. LINK. PDF of the
paper.
Lemmerhirt, D. F., Cheng, X., White, R. D., Rich, C. A.,
Zhang, M., Fowlkes, J. B., and Kripfgans, O. D., “A 32×32 Capacitive
Micromachined Ultrasonic Transducer Array Manufactured in Standard
CMOS”, IEEE Transactions on Ultrasonics, Ferroelectrics, and Frqeuency
Control, 59 (7), pp. 1521-1536, 2012. PDF of the
paper.
Doody, C., Lemmerhirt, D., Cheng, X., Collin, R., White,
R. D. “Modeling and Characterization of CMOS-Fabricated Capacitive
Micromachined Ultrasonic Transducers”, Journal of
Microelectromechanical Systems, v. 20, n. 1, pp. 104-118, 2011. PDF of the paper.
MEMS Microphones
A microelectromechanical systems (MEMS) based microphone array on a chip has been developed and applied to aeroacoustic measurements. The array is designed to measure the fluctuating pressures present under a turbulent boundary layer (TBL). Each chip measures 1 cm2 and contains 64 individually addressable capacitively sensed microphones, with a center to center pitch of approximately 1.25 mm. Surface topology, including the packaging, is kept to less than 0.13 mm. Element to element sensitivity variation in the array is less than 12.5 dB from least to most sensitive, and phase variation is less than 16.5 degrees (at 1 kHz). The microphone 3dB bandwidth is 300 Hz to 100 kHz, and the microphones are linear to better than 0.3% at sound pressure levels up to 150 dB SPL. A unique switched architecture system electronics and packaging method are employed to reduce data acquisition channel count requirements, and to maintain a low surface roughness.
The array was recently applied to the measurement of multi point turbulence spectra under a flat plate TBL in a low speed, low turbulence intensity wind tunnel at the University of Toronto Institute for Aerospace Studies (UTIAS). Testing was at a maximum speed of 30 m/s, and maximum Reynolds numbers based on plate length of approximately 106. Evidence of turbulent structures was gathered by examining coherence data between rows of array elements spaced apart in the flow direction. Coherence decreased with distance in the 300 Hz to 2 kHz band, indicating an ability to separate turbulent structures from acoustic pressure fluctuations in this band, even at the low speeds achievable in the UTIAS tunnel.
![]() |
![]() | |||
Prof. White in the UTIAS tunnel. The MEMS microphone array is visible in the floor of the tunnel. The array includes 64 microphones in a square grid over a 1 cm x 1 cm aperture. Testing was carried out with partners from Bombardier Aerospace and the University of Toronto. |
Microscope picture of one of the 0.6 mm diameter elements in the MEMS array. |
Representative Publications:
Krause, J., Gallman, J., Moeller, M., and White, R. D., “A
Microphone Array on a Chip for High Spatial Resolution Measurements of
Turbulence”, Journal of Microelectromechanical Systems, vol 23, n 5,
pp 1164-1181, 2014. LINK PDF
Zhao, Z, Krause, J.S., Liu, S.,Shin, M., Kastor, N., Lewis, P., and White, R. D. “Flow Sensing in Aerospace Applications” at the International Microelectronics and Packaging Society, New England, 40th Symposium & Expo, Boxborough, MA, May 7, 2013.
White, R.D., Krause, J., De Jong, R., Holup, G., Gallman, J., and Moeller, M. “MEMS Microphone Array on a Chip for Turbulent Boundary Layer Measurements” at the AIAA Aerospace Sciences Meeting, ASM 2012, Nashville, TN, Jan 8-12, 2012, AIAA 2012-0260. PDF of the paper.
Microelectronics and MEMS Packaging
Our group gets involved in a variety of electronics packaging problems, often either as we try to package our MEMS sensors, or as we work with partners such as Draper Labs on system packaging problems.
Aerosol Jet Printing of Transceiver Circuit
with Peter Lewis, Brian Smith and others at Draper Labs
This research employs aerosol jet printing to rapidly manufacture a multilayer PCB with COTs component integration. Specifically, this research provides a method to making a system-on-a-chip (SOC) circuit on a variety of substrates with novel integration methods. This fits well into the recent research phenomenon deemed “Internet of Things” (IoT). By advancing the manufacturing capabilities for a system that can measure and transmit data, one can integrate such circuits with minimal spatial and geometric interference to the broader device. A unique manufacturing process was developed for non-embedded components which involves the building up of the circuit around the system’s microprocessor. The transceiver circuit and its microprocessor, based off a commercially available circuit, has been successfully programmed and has shown to be working. The matching network is still being worked on, however, the goal is to have it working by the conference. To the best of the researchers’ knowledge, this research is novel in that it is the most complicated multilayer circuit that has been built using aerosol jet printing technology. Rapid ageing tests for a silver and a CNT ink were done and analyzed to determine the reliability of an aerosol jet printed circuit board. Results show adhesion is the primary mechanism of device failure as opposed to conductor degradation.
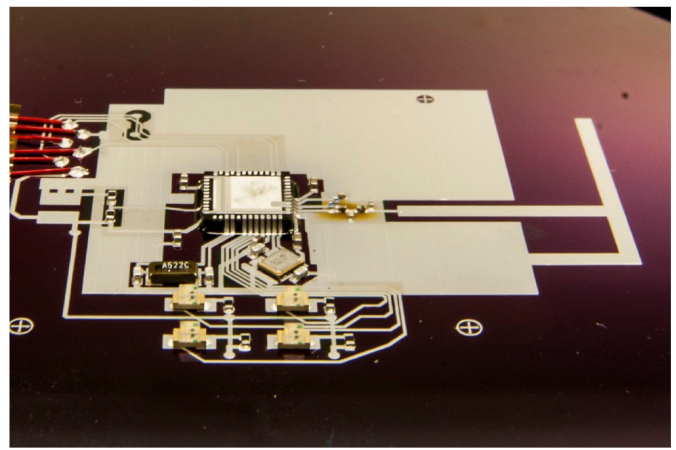
Image: A microcontroller and RF transceiver circuit created entirely using aerosol jet printing of both dielectric and interconnect layers.
Co-fabrication of Micro-Coaxial Interconnects and Substrate Junctions for Multi-Chip Microelectronic Systems
with Daniela Torres, Caprice Gray, Tony Kopa and others at Draper Labs
Low inductance micro-coaxial cables for power distribution as well as micro-coaxial cables for signal distribution have been fabricated using an in-situ fabrication and attachment strategy. These cables have been fabricated to expedite characterization of different wires for the Miniature Multi-Wire Systems (MMS) IR&D at Draper. MMSmain goal is to create a microelectronic packaging technology that will greatly reduce the time required to design and fabricate multi-chip modules and other complex electronic assemblies. This technology will be based on the use of shielded micro-wires (micro-coax) for all component interconnects to eliminate the lengthy layout and fabrication processes associated with today’s high-density packaging technologies. The first type of cable is a low inductance cable made with 1 Mil wire bonded Gold, 1 5m Parylene dielectric, and 5 5m Gold shield. The second set of cables are also low inductance cables made with 1 Mil wire bonded Gold, 100 nm Hafnium (HfO2) dielectric, and 5 5m Gold shield. The third set of cables are signal coaxial cables made of 1 Mil wire bonded Gold, 38 5m of Parylene dielectric, and 5 5m Gold shield. The characteristic impedance of these wires are measured to be 2.0-3.5O Ohm, 0.07-0.13O Ohm, and 44.6-51.5O Ohm respectively. Further characterization of these wires will also be discussed in this presentation, which will include cross-talk integrity and thermal shock reliability.

(Left) SEM image of the attachment end of a micro-coax wire where the core has been exposed for contact. (Right) SEM of a FIB cross-section of the micro-coax showing the shield, dielectric, and core.
Representative Publications:
Daniela A. Torres, Anthony Kopa, Robert D. White, and Caprice Gray, “Co-fabrication of Microcoaxial Interconnects and Substrate Junctions for Multi-Chip Microelectronic Systems” in IEEE Transactions on Components, Packaging and Manufacturing Technology, Early Access January 2020. https://doi.org/10.1109/TCPMT.2019.2955553
Peter Lewis, Robert White, and Brian Smith, “Lessons Learned in the Implementation of Aerosol Jet Printing for Fabricating Multilayer Circuit Boards” in Advancing Microelectronics Magazine: May 2017, Vol. 44, No. 3, pp. 12-15.PDF of the paper (1.3 MB).
Daniela Torres, Anthony Kopa, Robert White, and Caprice Gray, “Co-fabrication of Micro-Coaxial Interconnects and Substrate Junctions for Multi-Chip Microelectronic Systems”, in the iMAPS New England 45th Symposium and Expo, May 1, 2018. [Best student paper award.]
Robert D. White, Peter Lewis, and Brian Smith “Packaging of MEMS for Aerodynamic Measurements” in the 43rd iMAPS New England Symposium and Expo, Boxborough, MA, May 3, 2016. Invited talk.
Peter Lewis, Brian Smith and Robert D. White, “Printed Transceiver Circuit for System-on-chip Sensor and Processor” in the 43rd iMAPS New England Symposium and Expo, Boxborough, MA, May 3, 2016.
Robotics
Students: Martin Majkut, Nikolas Kastor
Our group has recently been working on two concepts in robotics. The first is design and control of soft foam robots. A motor tendon actuated soft robot was built from castable polyurethane foam with a low cost and robust manufacturing method. This method can produce a robot in less than one hour with lower cost and greater durability than 3D printing. The robot produced by this method exhibits the ability to change shape, by compressing and folding, allowing it to perform complex locomotion. Hard components, such as motors and sensors, are sutured into cavities in the foam body in order to facilitate the construction process and reduce interaction with the soft body. This highly deformable robotic platform will be useful in evaluating factors that affect locomotion including material selection, structural design and control methodologies.
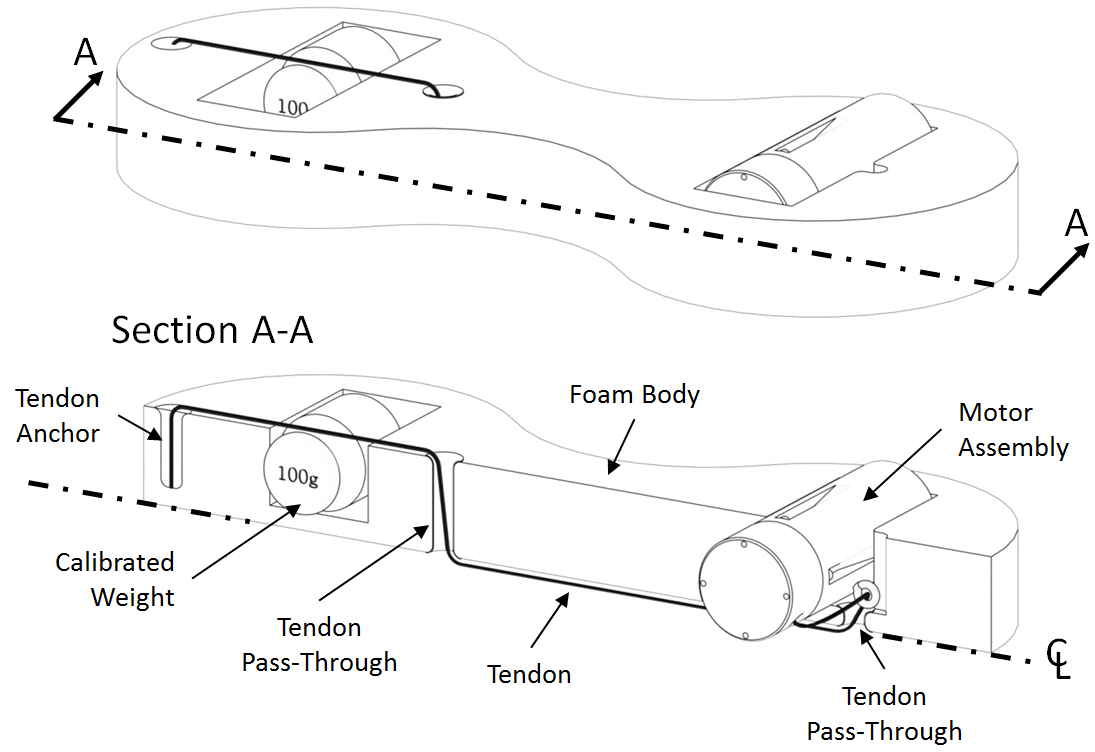
A tendon driven foam robot design. The calibrated weight is critical for controlling ground interaction and variable friction. Read the paper!
The second topic we worked on recently is vibration communication and sensing in robots. Structure-borne vibrations in a one dimensional structure were examined as a means of communication and sensing for networks of robots. The concept was inspired by the observation that insects use structural vibrations to communicate and to detect features of their environment. A 12 x 5 x 6 cm mobile robot capable of traversing an acoustically favorable structure was developed. A technique for measuring distance between robots and communicating commands to robots using vibrations generated on a common one dimensional substrate were demonstrated

The autonomous robot pictured was developed to navigate a rail system (one-dimensional environment). The robot can communicate with an external computer and sense distance by sending structural vibrations along a “third rail”. (a) Robot navigating the track (b) a close-up of the three-rail system (c) a cross-section of the rail system with labels.
Representative Publications:
Nikolas Kastor, Ritwika Mukherjee, Eliad Cohen, Vishesh Vikas, Barry Trimmer and Robert D. White, “Design and Manufacturing of Tendon Driven Soft Foam Robots” Robotica, vol 38, no 1, January 2020. Published online by Cambridge University Press, May 15, 2019. https://doi.org/10.1017/S0263574719000481
Nikolas Kastor, Vishesh Vikas, Eliad Cohen, and Robert D. White, “A Definition of Soft Materials for Use in the Design of Robots”, Journal of Soft Robotics, vol 4, no 3, September 2017, pp. 181-182. Letter to the editor. https://doi.org/10.1089/soro.2017.29012.nka
Nikolas Kastor, Ritwika Mukherjee, Eliad Cohen, Vishesh Vikas, Barry Trimmer and Robert D. White, “Locomotion of a Simple Foam Robot” in the 8th International Symposium on Adaptive Motion of Animals and Machines, AMAM 2017, Sapporo, Japan, June 27 – 30, 2017. Paper PDF
Cassandra M. Donatelli, Zachary T. Serlin, Piers Echols-Jones, Anthony E. Scibelli, Alexandra Cohen, Jeanne-Marie Musca, Shane Rozen-Levy, David Buckingham, Robert White, and Barry A. Trimmer, “Soft Foam Robot with Caterpillar-Inspired Gait Regimes for Terrestrial Locomotion” in the 2017 IEEE/RSJ International Conference on Intelligent Robots and Systems (IROS 2017), Vancouver, CA, September 24-28, 2017.
Nikolas Kastor, Lloyd Hill, Vishesh Vikas, Robert D. White and Barry Trimmer, “Semi-autonomous Soft Robotic Platform for Terrestrial Locomotion” in the workshop on New Frontiers and Applications for Soft Robotics at the IEEE/RSJ International Conference on Intelligent Robots and Systems (IROS 2015), Hamburg, Germany, September 28 – October 03, 2015. PDF of the poster (1.3 MB).
Maxwell Hill, Prasong Mekdara, Barry Trimmer, Robert David White, “Structural Vibration for Robotic Communication and Sensing on One-Dimensional Structures” in the 2015 IEEE/RSJ International Conference on Intelligent Robots and Systems (IROS 2015), Hamburg, Germany, September 28 – October 03, 2015. PDF of the paper.
Lloyd Hill, Prasong Mekdara, Barry Trimmer, and Robert David White, “Structural Vibration for Robotic Communication and Sensing on One-Dimensional Structures”, in the 7th International Symposium on Adaptive Motion of Animals and Machines (AMAM 2015), Cambridge, MA, June 21-25, 2015. PDF of the poster (1 MB).PDF of the paper.